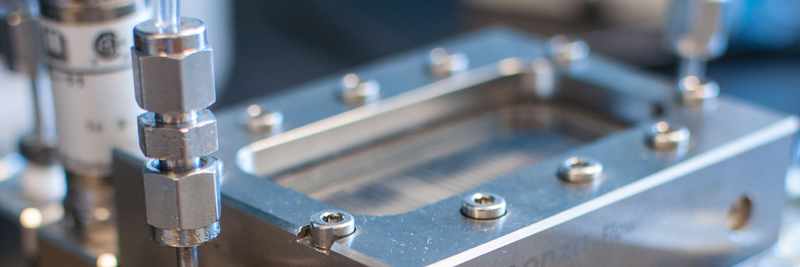
Available technology
Available technology
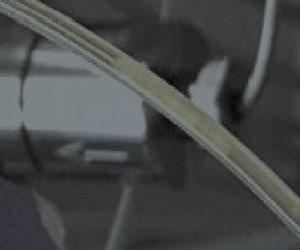
Slurry-handling LSVs
The ability to monitor a flowed reaction irrespective of how hazardous the sampling technique empowers process chemists to make critical decisions on the process. Typically a two-position LSV is sufficient to divert a portion of a flowed stream into a sampling loop. As long as the critical process parameters (e.g., pressure, temperature, and flow-rate) of the flowed stream are not impacted, online sampling can reveal a wealth of information on the ongoing process and mitigate the risk of losing a batch. However, typical two-position valves that direct flow to a sampling loop using a standard off-the-shelf valve fails to sample reliably as the narrow space of the configurable flow-paths inside the valve get clogged with solids.
A standard two-position valve controller can be uniquely customized to derive multiple degenerate valve positions for the load and inject configurations like any other standard LSVs. The multiple degenerate positions are used to systematically service clogged passage(s) during sampling. The unique valve controller method maintains process flow through an alternative passage while the clogged passage is being serviced in the new method. Additionally, we equip LSVs with inline filters and other sample purification tools to ensure that the output from the LSV is clean and injectable for online analysis.
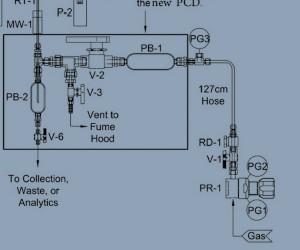
BPR-less pressurized flow reactor technology
Unlike batch chemistry, reagents have a short tenure at the energized zone in flow format. More importantly, reagents must exit the reactor through the outlet of the reactor tube at a steady flow-rate. Limiting the tenure of the reagents (and the product) within the boundary of the reactor tube brings a myriad of benefits, from limiting degradation of the product into by-product(s) to enhancing overall process safety. However, conducting a flow reaction under pressure and extracting the product out of the pressurized reactor without depressurizing the reactor tube is challenging. One common technique to accomplish both (flowing under pressure and liberating product) continuously uses constricted flow-path (e.g., a BPR) downstream of the energized zone. The back-pressure from the constricted path forces the reagents to stay energized within the confinement of the reactor. The BPR holds the liquid reagent in its liquid state even when the reactor temperature exceeds its boiling point. However, a BPR device comes with its own demerits. A stream that carries solids or a viscous matter struggles to move through the restricted flow-path of the BPR and often experiences over-pressurization due to clogging. Downstream cross-contamination between experiments is also a major drawback of BPR-based pressurized reactors.
We build pressurized flow reactors that maintain fluid communication with a remote pressure ballast, which is pressurized using an inert gas, to hold energized reagents within the energized zone of the reactor. This unique flow pressurization technique does not use any constricted flow-path as a part of the reactor and is compatible with reagent streams that may include solids. It is important to note that the internal pressure and the pressurization mechanism of the pressure ballast is programmable so you can modulate pressure inside the reactor as situations necessitate either manually or through a closed feedback loop.
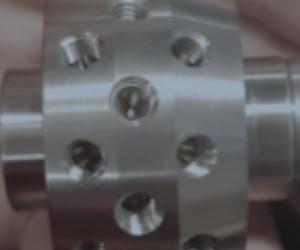
Multi-function LSVs
It's quite common to have an array of valves in a process workflow in order to orchestrate complex fluid movements through a reactor network. Various parts of the reactor network are kept under different pressures based on the nature of the fluid occupying individual reactor parts and the process condition the fluid is under. Consequently, when a particular valve turns to execute a fluid diversion function, the pressure ripple travels from one reactor part to another based on the pressure differential. High synchronicity in valve actuation is critical to arrest such pressure ripples so as to not disturb the pressure equilibrium in the entire fluid system. We assist researchers with custom-designed valve stators that connect to various parts of the reactor and deliver individual valve functions from a single valve-drive motor. This solution saves cost, reduces complexity in coding, and eliminates pressure ripples due to the asynchronous valve actuation.
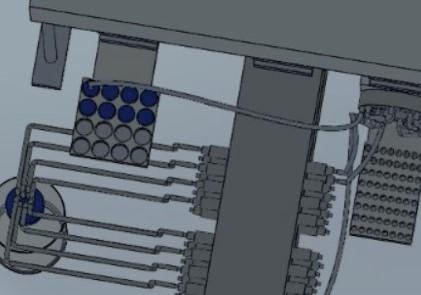
Online robotic sample extraction and preparation
One of the common techniques for extracting IPC samples from an automated flow reactor includes flow-cell. The flow-path inside the flow-cell maintains fluid communication with the reactor at all time. A pierceable membrane, which constitutes a barrier that holds the liquid inside the flow-path, allows for a syringe with a needle to aspirate IPC samples from the flowing stream. While the flow-cell technique has been in practice for many chemical and biochemical applications for decades, the pressure rating of the membrane limits the overall pressure tolerance of the flow reactor. Alternatively, an LSV can also extract an IPC sample from a flow reactor into a sampling loop. The isolated IPC sample can then be directly injected into an analytics. However, if the IPC sample requires a chemical treatment before the sample can qualify as an injectable, the IPC sample needs to be dispensed into a sampling vial first using an LHR or an autosampler. The cost of such an LHR rises rapidly as the LHR gets equipped with multiple robotic arms (one for analytical injection and at least one other for dispensing fluids into the sampling vial). We developed two unique solutions to make such complex fluid management possible from a single arm LHR/autosampler devices in collaboration with an LHR manufacturer. The first solution includes a programmable injection syringe that consists of at least one port on the side of the syringe which allows IPC samples to pass through when the port is opened from a remote controller. The second option includes a programmable robotic arm that grips various liquid-handling objects on command from a remote station.
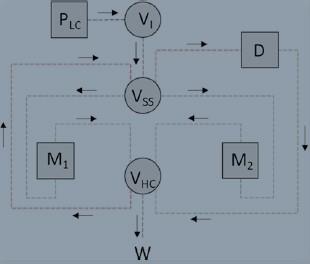
Multi-attribute process intensification
Many processes rely on multiple CQAs. These CQAs often require conflicting set of process parameters for an optimal performance. For example, a set of process parameters that give the best process throughput (yield) in the manufacturing campaign of a chiral API is often not well suited for the best chiral selectivity (ee). It is important to measure all CQAs in parallel during process development in order to make an informed decision during process intensification following the guideline of QbD principles. Measuring multiple attributes from a flowed process won't have to be sample size, cost, or time limiting. We can help you utilize a unique recirculatory multi-attribute process intensification platform that will allow you to measure all CQAs by recirculating a single sample for a multiple time through a custom chromatographic network until all aspects of analysis are judged complete.

Closed feedback loop
Automation has become part and parcel of modern life from being driven to work in an autonomous vehicle to overseeing production from an offsite location. Any automated platform is the ultimate display of how science and technology impact our daily life. But in order to accomplish such a scientific feat, a lot of information need to shuttle back and forth among machines in an efficient and effective manner. The M2M communication has become an essential component of automated continuous manufacturing. Without a robust M2M protocol, automation and AI cannot be implemented in a meaningful way. We can help you close the communication loop between fluid moving device(s) and fluid assessing detector(s) in the most flexible way so you can execute your process intensification tasks in an automated manner and/or deploy any algorithm of your choice from a remote site.