At present, many manufacturing processes are performed in batches. In batch format, all reagent molecules that are destined to give a product are held in confinement within the boundary of an energized batch reactor. The product molecules are kept inside the energized zone until the reagent molecules are consumed to maximize yield. The size of the reactor grows as the demand in the product in question goes up. Unfortunately, the uniformity in the distribution of energy drops as the dimension of the reactor expands. The drop in the orderliness of energized reagent molecules ultimately adds to the uncertainty in batch manufacturing. Flow chemistry provides a means to maintain orderliness in the reagent-product distribution across a reactor tube, which can be energized as per the need of the process. The process throughput due to the reduction in the length of the reactor tube can be compensated conducting a production campaign for a longer period of time. We can conduct a flow production run in killogram quantities using the same reactor that we use to make grams of the product. Furthermore, the residence time of the product inside the energizable zone of the reactor can be modulated by adjusting net flow-rate of matter flowing through the tube. This safety-by-design aspect of the flow format gives us confidence to leave reactions unattended as long as we can monitor the state of the reactor and train a computer to make decisions. Making decisions on reactions is relatively simpler in the flow format due to the inherent orderliness of the reactant(s) and the product across the length of the reactor tube.
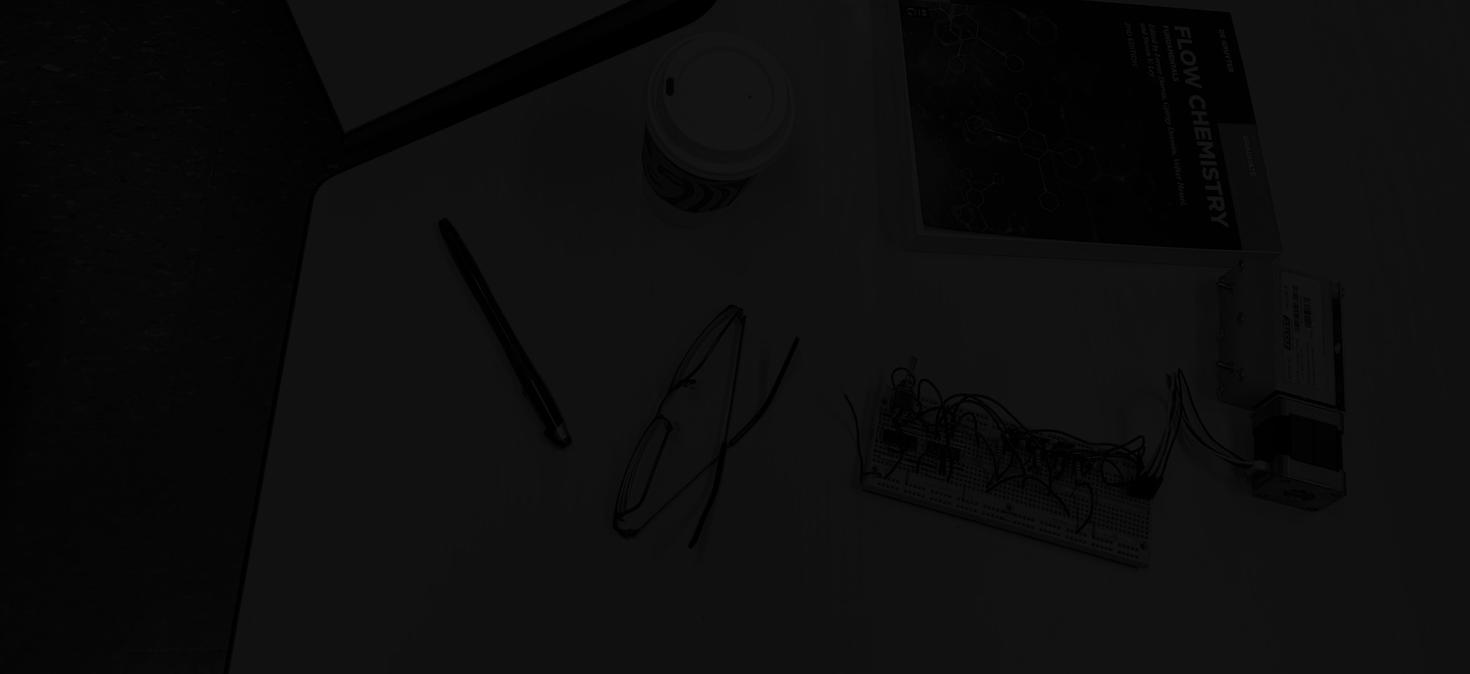
Collaborative research between uOttawa and YorkU
Sustaining the supply chain pipeline through remote and intelligent IoT reactor platform
If the current pandemic taught us anything, it is that nothing can be taken for granted. Over the past few decades, process chemists have made extraordinary strides in creating safe and efficient manufacturing processes for essential products, especially pharmaceuticals. However, difficulties remains when batches require large quantities of raw materials that are highly reactive or energetic, and consequently present challenges regarding safety and efficiency. Process scientists would traditionally be physically present at the production site and remain vigilant around the clock. No one wondered what would happen if we can't be physically present at the production site. Now we do. The recent pandemic forced us to question what we do in the manufacturing sector and how we do it.
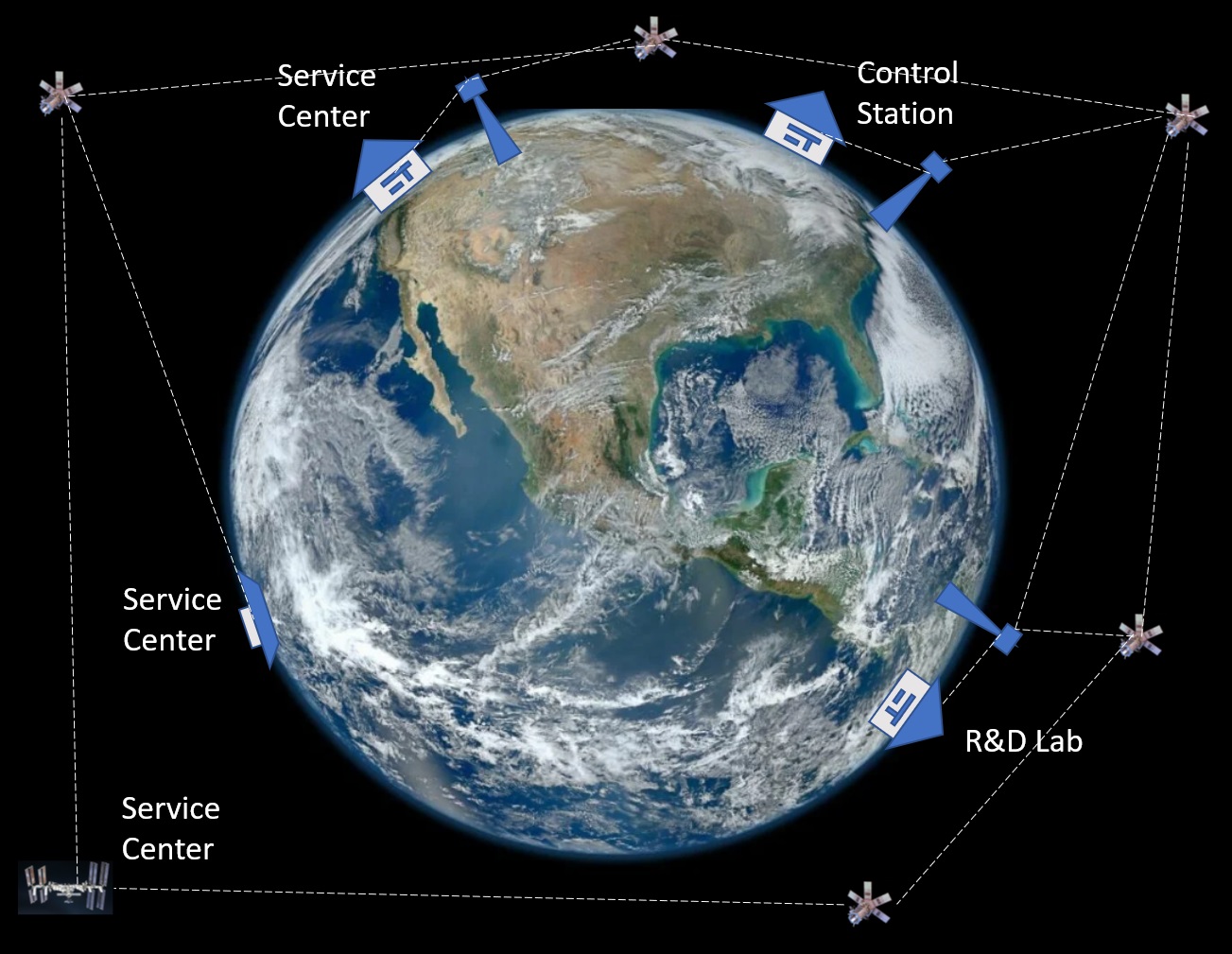
For these reasons, Prof. Michael Organ of the University of Ottawa, a flow chemistry expert, and Prof. William Pietro of York University, an expert of IoT for chemical applications, recently joined hands to build an IoT-enabled robotic reactor technology that can be controlled over the internet for process intensification and continuous process validation. The Flow Research Facility along with the manufacturers of liquid handling robots and fluid diverters has been building an automated synthesizer which can move reactive materials through an energizable reaction zone. The synthesizer is also capable of diverting a portion of the reaction matter for automated online and offline analysis. The York team is working on the M2M and the IoT communications for remote operation. The uOttawa team is focusing on the development of necessary PAT and analytical technologies for seamless and reliable performance of the platform, an essential component for remote operation. In addition, the uOttawa team is working on expanding the scope of application to human-free process intensification for medical diagnostics. Prof. Lora Ramunno, an expert in deep learning methods and AI, and Prof. Adam Shuhendler, an expert in radio tracer discovery and synthesis, would be working with the uOttawa team to transform this remotely controllable autonomous reactor platform into a medical diagnostic device for the production of radio-labeled tracers, which has the potential to greatly serve communities in remote parts of Canada. To learn more about the platform, or to find out how you can take advantage of our IoT reactor platform for your application please contact us.
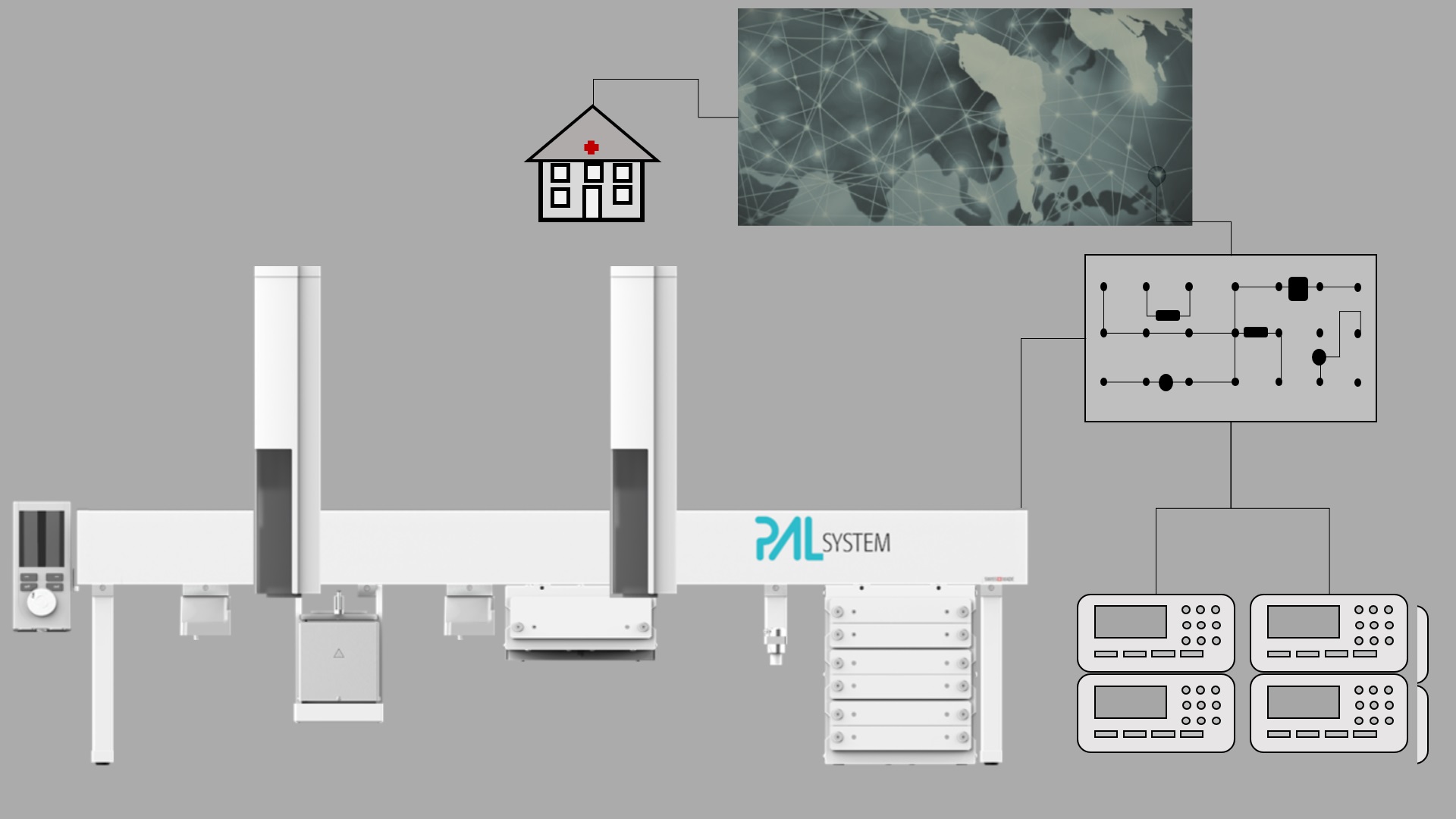
Current areas of application
- Autonomous Reactor Platform
- Remote Medical Diagnostics
- Long-haul Space Mission
- Supply Chain Solution